Introduction
At SK Steel Corporation, we take immense pride in being a leading Industrial socket weld flanges manufacturer with years of experience and a commitment to excellence, we have established ourselves as a reliable and trustworthy partner for businesses across various sectors. Our dedication to customer satisfaction and a diverse range of products has earned us a reputable position in the market. Socket Weld Flanges are an essential component in the piping and construction industry, providing a reliable and robust connection between pipes, valves, and other equipment. These flanges are designed to be welded to the end of a pipe, ensuring a secure and leak-proof joint, even in high-pressure and high-temperature applications.
The choice of flange connection is essential in the field of industrial engineering and plumbing systems for assuring the quality, safety, and effectiveness of the system. Socket weld flanges have become more common than other types of flanges because of their unique look and reliable performance. We will go further into the subject of industrial socket weld flanges in this extensive post, looking at their design, benefits, uses, and best practices.
Understanding Socket Weld Flanges
High-pressure flanges, such as socket weld flanges, are made to withstand the high pressures and temperatures that are common in industrial applications. These flanges are made with a counterbore that supports the pipe’s outside diameter and a female socket that slips over the pipe. The pipe and socket still have a tiny opening, which is filled using a fillet weld to complete the connection. This welding process offers high strength and performance without leaks.
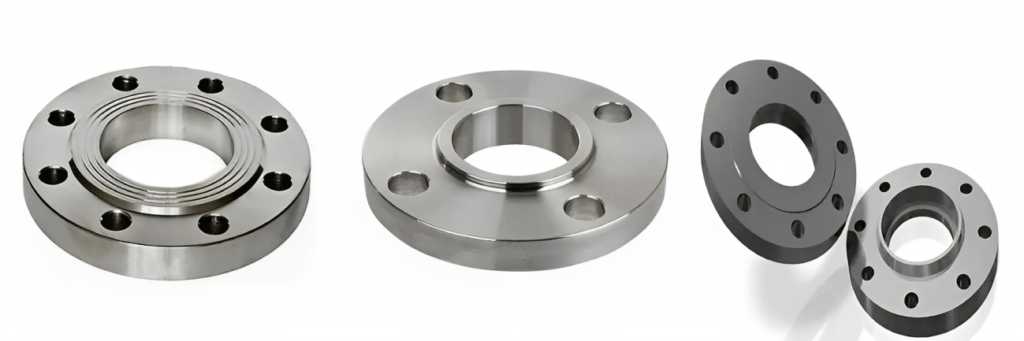
Advantages of Socket Weld Flanges
Exceptional Strength: Due to its higher strength, socket weld flanges can withstand high temperatures and pressures. A solid and dependable connection is ensured by the fillet weld at the socket’s base.
Leak-Free Performance: With socket weld flanges, the welding procedure produces a strong seal that reduces the possibility of leaking. This is especially helpful for systems where fluid containment is important.
Space-Efficient Design: Because they don’t need a lot of threading or flange faces, socket weld flanges feature a compact design that conserves space in constrained pipe systems.
Smooth Flow: In pipelines, the smooth internal surface of socket weld flanges reduces motion and pressure loss, which can be particularly advantageous in situations requiring effective fluid flow.
Easy Installation: These flanges are relatively easy to install and do not require gaskets, reducing the chances of human error in assembly.
Applications of Socket Weld Flanges
Socket weld flanges find extensive use in a variety of industrial sectors, including:
Chemical Industry: For chemical processing facilities, where the quality of the system is crucial, socket weld flanges are appropriate due to their superior strength and leak-free performance.
Oil and Gas: Because they can withstand the high pressures and temperatures involved, socket weld flanges are frequently used for wellheads, pipelines, and refineries in the oil and gas sector.
Petrochemical Industry: Pipelines in petrochemical facilities are connected with socket weld flanges due to the strict safety and environmental regulations.
Power Generation: Power plants often employ socket weld flanges for their high-pressure steam and water systems, where reliability is of utmost importance.
Aerospace: Aerospace engineering relies on socket weld flanges for various applications, including hydraulic and fuel systems, due to their strength and ability to withstand extreme conditions.
Food and Beverage Industry: The hygienic properties of stainless steel socket weld flanges make them suitable for use in the food and beverage industry, particularly in dairy, brewing, and beverage processing.
Best Practices for Socket Weld Flanges
Consider the following best practices to guarantee the maximum performance and durability of socket weld flanges:
Material Selection: Choose the right material for the flanges to match the environmental conditions, such as corrosion resistance in chemical applications.
Proper Welding: The quality of the weld is crucial. Employ skilled welders and inspect the welds for cracks, voids, or defects to ensure leak-free connections.
Size and Pressure Rating: Ensure that the size and pressure rating of the socket weld flanges are compatible with the application’s requirements.
Inspection and Testing: Regularly inspect and test socket weld flanges to identify any potential issues before they become critical.
Proper Installation: Follow manufacturer guidelines for installation, paying attention to torque values and assembly procedures.
Conclusion
In several industrial applications where strength, leak-free performance, and space efficiency are crucial, socket weld flanges are a key component. They are a preferred option in a variety of industries, from petrochemicals to aerospace, because to their exceptional benefits and adaptability. Socket weld flanges protect important pipe systems’ integrity and safety when chosen, installed, and maintained properly. Socket weld flanges are anticipated to continue playing a crucial role in addressing the problems of the contemporary industrial environment as technology develops and industry needs change.